1. Overview of raw materials:
The potato tubers are cobblestone-like, and the number and thickness of tubers vary greatly among different varieties. Potato tubers contain high amounts of starch, but contain less protein and fat, and the starch content is 15 to 25%. Some of the unique properties of potato starch are not replaceable by other starches, so they are widely used in the food industry.
2. The process:
Potato—Hydraulic Conveying—Cleaning and Conveying—Secondary Cleaning—Cleaning to StoneLifting—Crushing and Separating (Curling Extrusion Milling Machine) —Desilting—Concentration Refining—Vacuum Dewatering—Airflow Drying—Finished Packaging
3. Process introduction:
The following is a brief introduction to the production process and equipment of
potato starch processing equipment from Goodway Potato Machinery.
1. Cleaning process and equipment
The main purpose is to remove the sediment from the outer skin layer of the material and wash away the skin of the root of the material. The stone cleaning machine is to remove the hard impurities in the material. Cleaning the raw materials used to produce starch is the basis for ensuring the quality of the starch. The cleaner the starch is, the better the quality of the starch. Conveying is the transfer of material to the next process. It is often transported while also having a cleaning function. Commonly used conveying, cleaning and stone removal equipment are: hydraulic flow tank, screw washing machine, oblique squirrel cage washing machine, paddle washing machine, stone removal washing machine, (flat) cage washing machine, rotary drum type washing machine, scraper conveyor, etc. According to the characteristics of soil and materials, some of them can be combined to achieve high cleaning purity and convenient transportation.
2. Raw material crushing and equipment
The purpose of the pulverization is to destroy the structure of the material, so that the tiny starch granules can be smoothly separated from the roots. The requirements for shredding are:
1. Break the cells of the material as much as possible and release more free starch granules.
2. Easy to separate. It is not desirable that the skin residue is too fine. The fineness of the skin residue is not conducive to the separation of the starch from other components, and increases the difficulty of separating the fine residue. Goodway has the leading sorting crushing at home and abroad. The material pulverized by the first level of grater is immediately filtered to reduce retardation. The second pulverization is carried out on materials that do not meet the requirements. The requirements are no longer comminuted, so that the fineness is uniform and the power is reduced. And the pulverization fineness has controllability, and can be adjusted according to the nature of the material. This is the ideal smashing method in starch processing.
3. Screening process and equipment
Starch extraction, also known as pulp separation or separation, is a key link in starch processing, directly affecting starch extraction rate and starch quality. The pulverized material is fine fibers. It is larger than starch granules. Its coefficient of expansion is also greater than that of starch granules. Its specific gravity is lighter than starch granules. The pulverized material is separated from the starch and the fiber by using water as a medium. Goodway uses a fully panning-pressureless percolation-squeezing process in a multi-stage cycle. Fully panning allows the starch to be freed from the fibers. The non-pressure diafiltration allows the slurry water to pass through the screen holes and the fine slag remains on the mesh. Squeeze to further filter out the starch slurry water contained in the fiber. Starch extraction can be accomplished with less power and a quicker process.
4. Washing process and equipment
The washing and concentration of starch is accomplished by means of a starch cyclone. The cyclone is divided into a concentrated cyclone and a washing refining cyclone. After the sieving, the starch slurry passes through a concentration cyclone, and the bottom stream enters the washing and refining cyclone to finally meet the product quality requirements. The equipment is equipped with a complete automatic control system, using a high quality swirl tube and a more optimized piping scheme, so that the concentration of starch milk removed by the last stage cyclone reaches 23Be'. This is ideal for starch washing equipment.
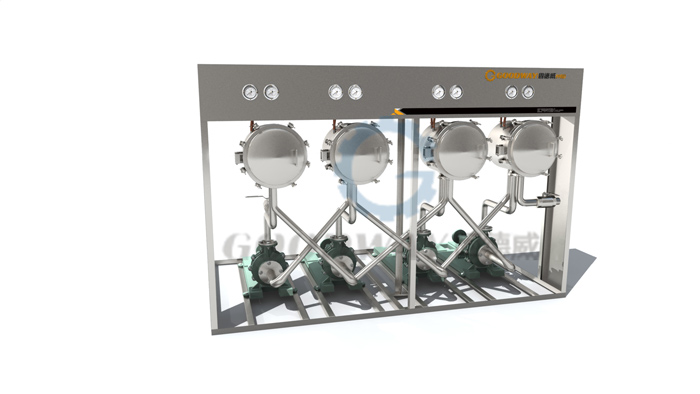
5. Starch dehydration
A vacuum suction starch dehydrator is used. The device also has a washing effect while dehydrating the starch. The utility model has the advantages of advanced structure, low energy consumption, good dehydration effect, convenient installation and operation, and stable operation. Automatic feeding, automatic dehydration, and automatic cleaning are possible. It is currently an ideal starch dehydration equipment in China.
6. Starch drying
The airflow starch dryer uses a high-speed flowing hot gas stream to suspend the wet starch therein and dry it during the flow of the gas stream. It has the characteristics of high heat transfer coefficient, large heat transfer area and short drying time.
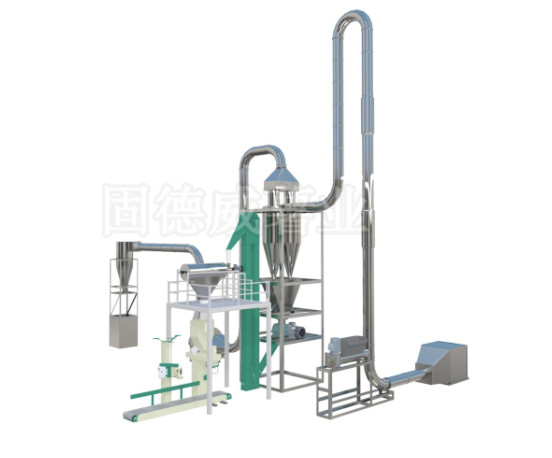
7. Starch cooling and sieving packaging
After the starch is dried, the temperature is higher. In order to ensure the viscosity of the starch, it is necessary to rapidly cool the starch after drying. Our factory uses a cold air system. The device has the advantages of low energy consumption, good cooling effect, stable operation and large processing capacity. The cooled starch enters the finished sieve and enters the final packaging process under the premise of ensuring product fineness and yield.
4. Main indicators:
This line processes 50-150 tons of fresh potatoes every day.
Potato raw material requirements: starch containing > 15%, fresh, no mold, no soil, stones.
Water supply requirements: turbidity <0.1, hardness <100, SO2 <0.55ppm, iron <0.9 ppm, no floating matter, pressure >0.2MPa.
The standard of finished starch: water ≤ 18 ~ 20%, fineness ≥ 99.6 (100 mesh pass), protein ≤ 0.1%, whiteness ≥ 90% (475mn, reflectivity), chemical SO2 ≤ 30ppm, ash ≤ 0.25, Spots ≤ 3. (fully in line with national first-class standards)
Water consumption: 2 to 3T per ton of fresh potato
Power consumption: about 200 degrees per ton of finished product
Coal consumption: about 2 tons of steam per ton of finished product
5. Civil construction requirements
The main workshop can adopt steel frame structure with a construction area of about 400㎡. The height is greater than 4m and the part is 13m. The material library, finished product library, and product library are not included. Auxiliary rooms and office buildings are self-determined. The total area of the factory is not less than 2,000 square meters.